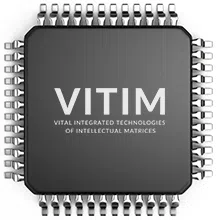
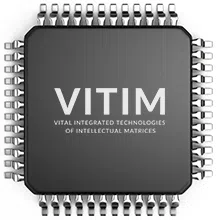
Agile
Integrated
Device
Laboratory
New Format of Microelectronics
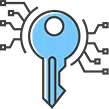
Design of IP-modules based on structural and technological basis of vacuum and combined electronics (vacuum + semiconductor electronics)
Re-engineering of IP-modules
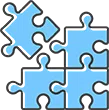
Structural and technological development of microchips
IP-tuning & re-engineering of microchips
Production of fully-featured superior devices SiP (System-in-Package), SoC (System-on-Chip)
Neuromorphic systems of artificial intelligence (AI)
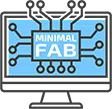
Foundry – tailored approach in chip production
Replication of own products
Production of experimental and pre-production batches
Laboratory tests
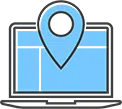
Comprehensive operation-wise delivery and sale of minimalFAB units to end customer with all pertinent component parts and consumables (within the region);
Commercialization and delivery of the technologies (synthesis of crystals, integrated turnkey production technologies)
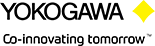
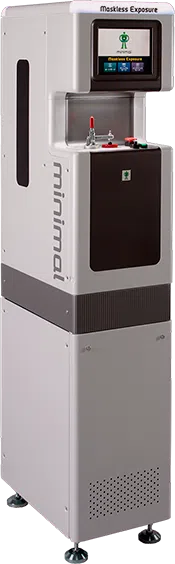
AIDL approach integrates scientific and engineering centers, design-center, single crystal growth and processing areas, and flexible production line of SoC (System-on-crystal) and SiC (System-in-Package).
minimalFAB is a set of space-saving high-tech units of 30cm in width, capable of processing wafers with diameter of 0.5 inches and producing various chips in small and medium numbers. Each technological process of a chip production is fulfilled using different minimalFAB unit. Processing time of a wafer on a single minimalFAB unit takes no more than 60 secs. The units are interconnected with robot manipulator, which carries out transportation of wafers in hermetic containers "Minimal Shuttle". The shuttle obviates the need for sterile rooms, expedites overall production process, and significantly reduces the expenses.
Mobile production laboratory of AIDL VITIM allows producing microelectronic tools on Si, Ge, GaAs, SiN, SiC substrates under the technology CMOS, CMOP, MEMS, NEMS, VIS and other advanced fields of electronics development.
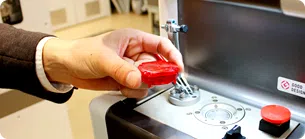
Waffle transportation is carried out in individual hermetic containers "Minimal Shuttle"
-
Tailored approach
-
Any batch to order
-
Short production time
-
Low production cost
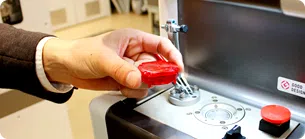
Waffle transportation is carried out in individual hermetic containers "Minimal Shuttle"
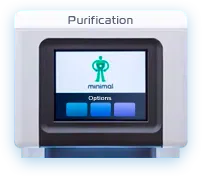
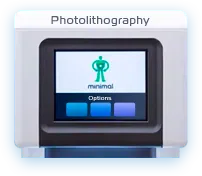
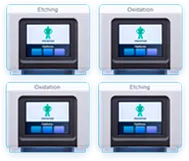
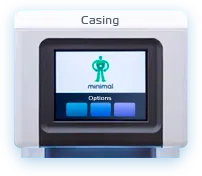
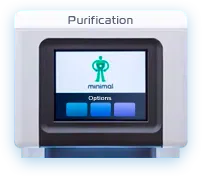
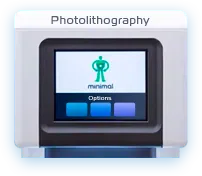
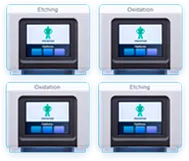
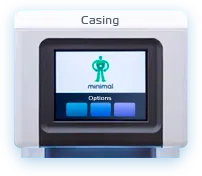